F-705 bulkhead
3h
August 26, 2025
Today I started working on F-705.
While waiting for an extra angle stock to try to improve one of the angles on the firewall, I started working on the F-705 bulkhead. This bulkhead uses a lot of stock material for various parts.
First, I made the little F-705H spacers. Since I have a small milling machine, I cut the stock in half (longitudinal, as per instructions), then milled it to the size. The best operations to remove the stock are drilling and sawing, so ideally you should size your stock close to the final dimensions, then mill it. However, I felt a bit lazy, so I just cut it in half and milled extra material off. Aluminum is a very soft metal, so it's not a big deal.
Final product. I kept these spacers a bit longer than necessary, so I can mill them after sizing them to the bars.
Then I drilled the holes in the center section F-705B bar. I took the approach I saw on VAF: instead of clamping it to the F-705A rear spar attach bulkhead and aligning the center to the holes to the line, I drilled a #41 hole in the very center first (find the center, center punch, drill). Then I used a cleco to attach it to the F-705A part.
This allows the bar to rotate and makes it much easier to align the remaining holes. I had a centerline on the F-705B bar, but I aligned mostly by "feel" on the opposite sides. Using the left and the right thumbs, rotate the bar such that both thumbs "feel" about the same distance from the edge of the F-705A to the edge of the F-705B. Verify the centerline is centered in the holes (I also verified by doing some measurements with the caliper), clamp it, then drill it.
I did the initial drilling on a milling machine, which made very good holes. However, at some point, I switched to the electric drill because placing the part on the milling machine was becoming tricky due to the clecoes.
This is where I made a small mistake. The very first hole I drilled with the electric drill grabbed the drill bit and scratched the part a bit with the drill jaws. I guess that's another reason to use proper aircraft drill bits which are 12" long. Also, a pneumatic drill (but it was very late, so I could not use it), which drills with much higher RPM and tends to grab less. I sanded the scratch mark off, measured the thickness with the micrometer, and it was, on average, 0.031" versus 0.032" in other areas, so should not be an issue.
Then I went to drill the F-705C bar doublers. I went with the following procedure.
First, I measured the dimensions and found that I only need to remove the material from the "short" outboard side (the side that is closer to the bend). The inboard side was on spot (on both of the doublers).
Then I measured 1/4" from the inboard side and put a line there -- this would be the location for the hole on the thin end. I clamped the doublers such that this line was centered in the hole. Actually, I cheated a bit and moved that line a bit inboard, so I get just a hair more than 1/4" of the distance, about 1/32" more. Since I have not shortened the part yet, I have some reserve distance on the outboard side.
Finally, I drilled the remaining holes. This was the moment I made another mistake. While drilling happily, I have not realized that one hole goes only through the F-705A and F-705B, but not through the F-605C (this is the hole that is opposite to the "slanted" section of the doublers). So, the drill went through and left a partially drilled hole on the F-605C doubler.
I researched the problem on VAF (yes, I should have researched all parts numbers before working on them), and it turns out this is a common mistake. The solution is to drill the hole and put a rivet in it, which is what I am going to do (unless I ruin the part and re-order it!).
The final result.
View from the back. Note that I have not shaped the doublers yet. Now that I have (almost, I still need to drill the holes for the bolts) all the holes in the doublers, I can cut off reliefs without risking violating the edge distances.

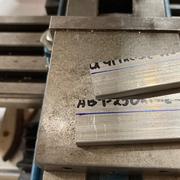
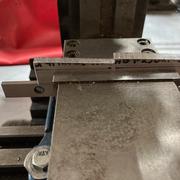
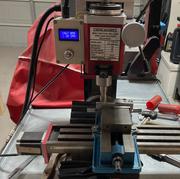
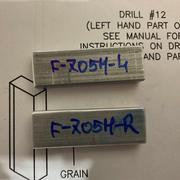
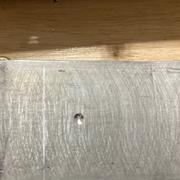
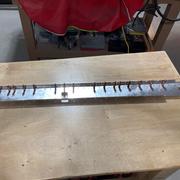
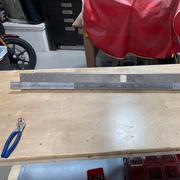