Riveting firewall together
4h
August 26, 2025
The last step was to rivet firewall parts together.
Today I riveted the firewall together. However, before that, I received "mock" batteries from EarthX: "C" case and "E" case. They are just plastic boxes that could be used for fitting batteries.
I ordered them to figure out the future work to install batteries. The was a report on VAF saying that you will have to redo some work and also will need to resort to counter-sinking (instead of dimpling) when installing some of the parts in the future. After researching what kind of work will be done in the future, I concluded that I don't need to plan for it. Too many unknowns.
In some cases, it would be removing some rivets and upsizing the hole for the bolt. In other cases, I will need to countersink to install nut plates, but since I use NAS1097 rivets for nut plates, I will countersink either way. In both cases, it seems okay to redo some work.
So I decided to install every single rivet and then modify it as necessary in the future.
However, I like the size of the "C" case: it is very compact. Since I plan to install two batteries, any space I can save is good.
Then I proceeded to rivet the parts together. I squeezed all perimeter rivets which I could access with the manual squeezer. After that, I back riveted everything else.
The hardest rivets were the ones that attach F-601J angles to the F-601N stiffeners: there was very little space so my back riveting set did not fit. In the end, I bucked them the normal way, with the flat set and the bucking bar. They came out ugly, but acceptable. A few of them are on the smaller size (the pressure was a bit too low so I hardened them a bit instead of swelling), but still larger than the minimum 0.163".
One rivet I drilled two times before I got an acceptable result. So I ran out of AN426AD4-9 rivets in the end (there were only a few spare ones).
Interestingly, the plans use both AN426AD4-8 and AN426AD4-9 for attaching these angles even though the thickness is the same everywhere (and yes, even though AN426AD4-8 give acceptable result, they are on the smaller side).
The completed firewall bulkhead.
The view from the back.
Finally, I drilled two holes that are used later to attach a motor mount. I drilled the holes with a #40 drill bit first, for which I used a drilling bushing I made before. It worked fine for the first hole, but the second hole came out extremely crooked. I think, the drill bit grabbed while drilling: the hole goes exactly between two parts under the mount so there is a narrow gap between them.
Luckily, I used a #40 drill bit, so I was able to use a small file to straighten the hole and upsize it to a #14 drill bit, then use a #12 reamer to clean it. The plans call for a 3/16" size, but the #12 reamer is close enough (0.189" versus 0.1875").
The very last thing I did was I filed two holes in the recess that did not match with the firewall holes to make it possible to insert a rivet through them. The holes are definitely oversized now, but since the recess is stainless which is much stronger than aluminum, I think, it is okay. The underlying firewall sheet and the stiffeners have correctly sized holes.
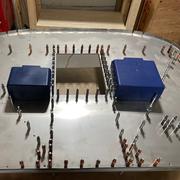
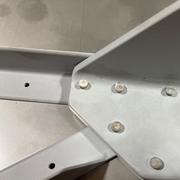
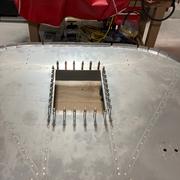
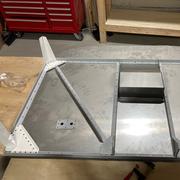
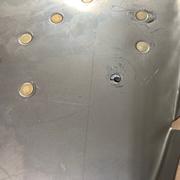
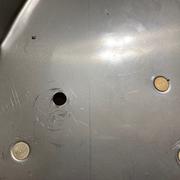
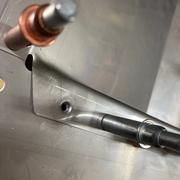