Forming block for the F-711B
3h
August 26, 2025
Since I want to try replicating the F-711B part, I made a forming fixture.
I started by disassembling the F-711 bulkhead assembly into the parts. Getting rivets out of the F-711C bars was a bit of a challenge, I had to drill them through with a small drill bit and use a hammer to knock them out of the holes. However, in the end, I disassembled everything without damaging holes. Damaging too much anyway, I haven't done a careful inspection yet. F-711A got a few scratches but otherwise looks good.
Then I prepared the F-711B part, so I can make a forming block from it. I made flanges to be 90° degrees and I unbent all the flanges that correspond to the J-channels and the longerons. The reason I unbent these is that they are offset just a tiny bit into the part, and it will make it harder to make the forming block profile. Without them, the profile is trivial: square part with a round bottom.
Then I used oak from Home Depot to make a forming block. I made a rough cut with the Jigsaw, then sanded it so that it fits into the part. This took probably about an hour to do. I started sanding with the 80-grit belt, then switched to the 120-grit for the final adjustments.
Here I made a small mistake. I drilled the tool hole in the block using the part as a template, but my mistake was that I did it before I made the block fit perfectly. As a result, the tooling hole in the final forming block did not align with the hole in the part itself. This will make it a bit harder to match the part with the F-711A. I could have used the tooling hole for that, but since it is offset, it won't match the tooling hole on the F-711A part. Not a big deal, I can align the part visually and use clamps to hold them together, then drill the matching holes using F-711A as a template.
Then I used a copying router bit to copy the forming block into another piece of oak to be used as a crushing block. Both blocks and the bolts holding them together make a forming fixture.
I haven't decided yet how to bend the tabs corresponding to the J-channels and the longerons. One option is to use a router to make small indentations where these tabs would go. J-channel indentations should be 0.025" and the longerons one should be 0.125", based on the thickness of the materials. However, it is not clear to me how to do the bending. Maybe, by pushing with the hardwood stick (and, possibly, hitting it with the hammer).
Another option is to cut a slit in a hardwood stick and then use the slit to bend the tabs "by eye".
Finally, I removed the primer from the bars using the lacquer thinner.
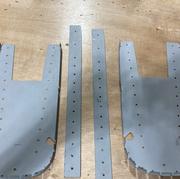
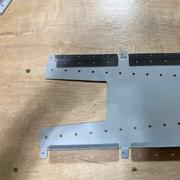

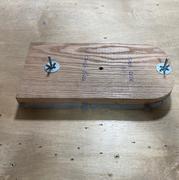
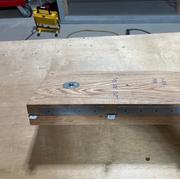
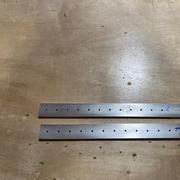