Finishing the horizontal stabilizer skeleton
6h
August 26, 2025
Today I fitted the remaining ribs and match-drilled the skin to the structure.
The first thing was to trim the HS-702 flange a bit more, so it does not interfere with the HS-00005 rib. I tried to estimate how much more do I need to trim. In the end I looked the original SB-14-01-31 which gave pretty specific dimensions (5/16" from the hole and 15/32" from the edge). I tried those, and they worked perfectly. I put the line on the flange and trimmed with my files, then finished with a small Scotch-Brite wheel. I used an electric drill instead of a die grinder so I don't make much noise, but it worked fine.
The next part was to fit HS-00005 and HS-00006 ribs, which looked very scary (and for a reason!). The funny thing is that once I have done it, it did not look that intimidating to me anymore. But then I started I tried to verify and re-verify every single step I was making. The first thing was to put ribs in place and mark the approximate holes locations.
Then, I fluted the ribs between those approximate locations. After that, I clecoed HS-00005 in place and drilled it to the rear spar.
The mistake I made here was that instead of making sure my center line is visible through the holes, I opted for aligning edges of the rib to the edge of the skin. I think, the lesson I should take here is that I should not generalize how parts fit together. I looked at the tip ribs and they were pretty much flush with the skin. So I thought that my inboard ribs should go in a similar manner (confirmation bias!). Well, it turned out that holes got a bit too close to the bend line.
I checked the MIL Spec again, and they give a special consideration for universal head rivets close to the bend radius. It should be 0.030" minimum from the bend radius tangent point. I checked my spacing, and I think I am good. Also, I think this side is going to be shop head which is going to be smaller compared to the factory head.
The next step was to match-drill the holes in the inboard tip rib to the front spar assembly. This went with no issues. And then, I was at the scariest point where I needed to drill through the splice / reinforcement angles, the front spar and the front spar doubler.
And this is where things did not go as planned.
The most embarrassing thing is that I knew there are a lot of the edge distance issues in these parts, so I've read these topics. However, I don't think I understood how these parts all work together. So I measured the distances given in the plans, re-measured them and then drilled it. And the hole was too close to the edge on the doubler part!
I think, this is what deceived me (confirmation bias again!): I saw holes lining up nicely, and instinctively aimed at that. I was kind of too afraid to move the hole to avoid getting too close to the edge of HS-710.
HS-710 looks good.
HS-702 looks good, too.
However, HS-00001 displays some signs of trouble. The distance is way too small! However, SB does allow for 5/32", which is 0.156", and I have 0.176". Kind of concerning, but still in spec?
Inboard aft rib, HS-00005, is what I was really concerned about. I estimated where hole would land, and got about the same distance as with HS-00001 doubler. However, this part is not as thick as the doubler!
I contacted Van's Aircraft support and initially their response was either to re-flange the rib (similarly to how it is done in the Service Bulletin), but with wider flange or to replace the parts.
I then asked what distance would be acceptable for the rib given that I cannot move it too far as I was concerned getting too close to the edge of the reinforcing angle HS-710. They told me that the edge distance is the same as for the HS-00001, 5/32".
I got confused because I estimated more than that? They answered that if I can keep the edge distance more than 5/32, I should be good.
So, I drilled the hole and got edge-to-edge distance of .103~. Which is somewhere about 0.167" edge distance from the center of the hole (the hole is the final size of #30). Not great, but should work?.. One thing that makes me a bit more comfortable with this decision is that both front spar and the reinforcing angle both have very good edge distances. And doubler is thick and is full of rivets.
I don't know anything about the rib flange, though. What are the forces there? Is the risk that hole would crack and the flange would rip open, leaving the rivet loose?
So I continued with the drilling, and fitted all of the ribs.
Finally, I drilled the skin to the skeleton.
Next step would be to disassemble everything, drill few remaining holes, prime and rivet!
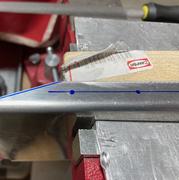
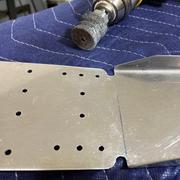
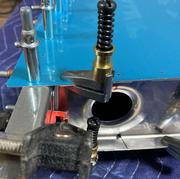
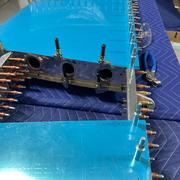
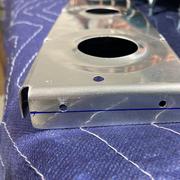
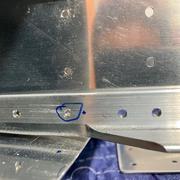
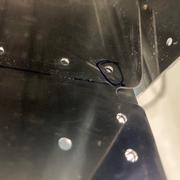
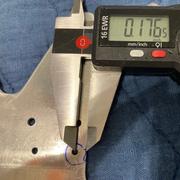
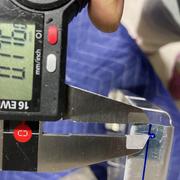
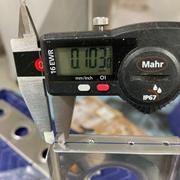
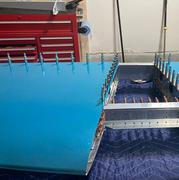
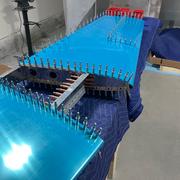
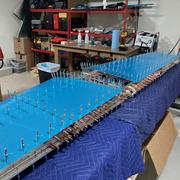
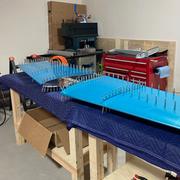