Fitting rudder together
2h
August 26, 2025
Today I started a temporary assembly of the skins to the skeleton.
First, I did a tiny part: nutplate strip, just because it only took me a few minutes. I opted to countersink holes for the "oops" sized rivets (NAS1097AD-3) using the deburring tool. It did leave some amount of chatter, though, but it should not matter as this application is not critical (these rivets are mostly to keep the nutplate from moving).
Then I put the skin to the skeleton and started drilling the holes.
Trimmed the horn brace. I knew that there might be edge issues with this part, so I left a generous amount of material (note the tooling hole on the edge). Plenty of edge distance!
Then I cut two attach strips from the raw stock.
The final step was to drill holes through the skin and rib into the attach strips. And this is where disaster happened. Since strips did not have any holes, I was not able to cleco skin and the rib together. Instead, I used cleco clamps. However, I did not notice that my rib moved slightly and holes on the rib were not fully aligned with the holes on the skin. After I drilled the holes through the attach strips, I got slightly oblong holes on the skin.
The most oblong hole has a larger diameter of ~0.122". I think my plan is to upsize these holes to the next size of the rivet, AN426AD4. There is enough edge distance on both the skin and the flange of the rib. However, on the attach strip the edge distance would be marginal: less than 2x, 0.250", but more than the minimum per MIL Spec, 0.219".
Another option is to use "oops" rivets, but I don't think I want the whole row of these: their heads are much smaller than the normal-sized rivets. Also, nothing is dimpled yet and dimpling for the "oops" rivet with the hole being upsized to #30 might be tricky.
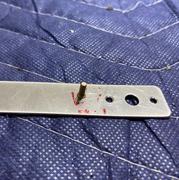
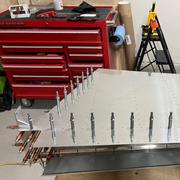
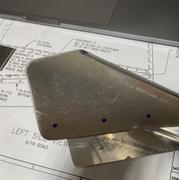
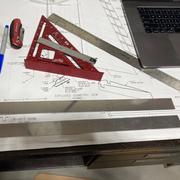
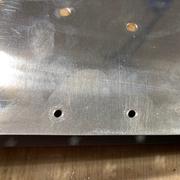