Dimpling the remaining parts and riveting the rudder
3h
August 26, 2025
Today I dimpled the remaining parts and started riveting the rudder together.
There was nothing special about the dimpling except that a few holes with very little space required a different technique. For -3 rivets I have a dimpling bucking bar I had a lot of success using. However, I did not have it for the -4 rivets, so I decided to try close quarters dimpling dies.
They kind of work, but I am not super excited about the resulting dimples. They don't center well as the nail I use is smaller than the hole. Other than that, they work okay.
After dimpling everything, I started assembling the rudder. The first steps were to install reinforcing plates and nut plates.
I was kind of too lazy to set up the pneumatic squeezer, so I went with the manual squeezer (where you have less risk of damaging the part if something goes wrong). I found that I like it more: it is very light and easily controllable. You can always stop in the middle of the squeeze if you are squeezing too much or if the rivet gets crooked. There is no danger of accidentally pressing the trigger and destroying something as with the pneumatic squeezer (well, it has a "safety" lock on the trigger, but I removed it early on as it was very awkward to use).
So far I found only two disadvantages:
- It requires more hands (or clamping parts) whereas with a pneumatic squeezer you can use one hand to hold the part and the second hand to push the squeezer and press the trigger.
- 4" thin-nose yoke I have does not work with the manual squeezer as it requires a longer set holder. Even my longest flat die does not extend the die enough to squeeze short rivets.
Installing the rudder horn brace was interesting. I believe you can use blind rivets for the whole part (LP4-3 for the AN470AD4 rivets and CS4-4 for the AN426AD3), however, as it turns out, the whole in the brace is located very strategically and can be used to access at least AN470AD4 rivets.
You squeeze blind, but with the longeron yoke, no problem! Push the squeezer against the factory head, peek through the hole to see if the flat die sits square and centered on the rivet end, then squeeze.
Rivets turned out to be fine, although, it's hard to see them.
Then I proceeded with riveting the counter-balance skin. This is where I used my pneumatic squeezer because I could only access counter-balance rib rivets with my 4" thin-nose yoke. The hardest rivets were the two rear furthest rivets out of the six rivets connecting the counter-balance skin to the rudder skin. The issue was that there was not enough space for the yoke. I could have bucked them, but it was late and I did not want to make noise.
So, the trick is to partially close the squeezer, then push it such that the rivet sits flush. The problem is that you cannot reliably keep the squeezer partially closed by feathering the trigger: it's too risky. You press too hard and it either slips off the rivet and damages parts or sets the rivet such that it does not sit flush.
As before, I removed the spring which allowed me to position the squeezer on the rivet. It does not let to fully push on the rivet but nevertheless keeps the rivet flush to the surface.
Finally, I decided to remove the primer from the outside of the counter-balance skins. Few minutes of rubbing the primer with the acetone and it is gone! Apparently, EkoPoxy is not very resistant to acetone, at least the next day after priming.
Another small task I did is to install nut plates on the counter-balance nut plate strip. I used NAS 1097 rivets to attach nut plates to the nut plate strip as they have smaller heads and counter-sinking could be done by turning the deburring tool just a few turns..
Also, I filed the counter-balance a bit so it fits without interfering with the rivets. I am not 100% confident it sits flat, though. I wanted to use screws to clamp it and see marks on the lead (since the lead is so soft, the rivet would leave a mark), but I don't have a nut to use with the #10 screws (and I cannot use nut plates since they will lock the screws).
At the end of the day, this is what the rudder looked like:
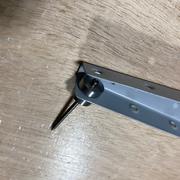
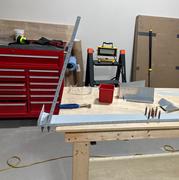
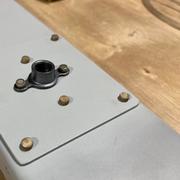
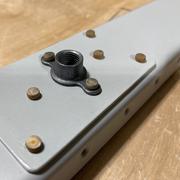
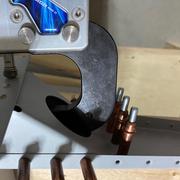
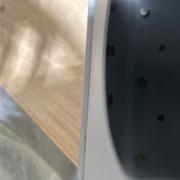
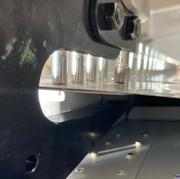
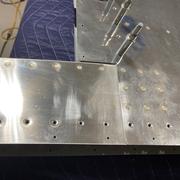

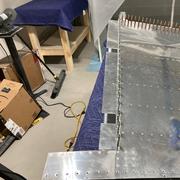