Folding the trailing edge
3h
August 26, 2025
Today I made a simple bender and bent both elevators trailing edges.
First, I made a simple bender from two pieces of 2x4 and a piano hinge. I put a hinge on the long sides so the short sides make the work, as I only needed to apply the pressure close to the fold. I attached two short pieces of 2x4 with the clamps so I can use them as handles to apply pressure.
Then I used the bender to fold the trailing edges of both the left and the right skins. Starting the bend was the hardest as I needed to apply a lot of force and also elevator was pushed away from the bender. To lock it in place, I clamped another long 2x4 directly against the leading edge of the stiffeners to stop the skin from moving.
The resulting bends were okay.
Here are some examples. The first location is okay.
This location looks a bit underbent. I need to fabricate a squeezing tool to finish it.
This looks perfect.
Then I clecoed the right elevator skin with the understructure and drilled all the holes. Per the manual, I needed to countersink the E-702 elevator spar at the place where the E-709 root rib attaches. The countersink is for the AN426AD3 rivets to sit flush so the elevator horn can sit on top of it.
I know some builders dimple both the E-702 and the E-709, but I don't want to dimple to avoid potential distortion from the dimples. I also don't feel comfortable countersinking all the way for the AN426AD3, which would likely leave me with a knife-edge in the hole. It probably does not matter that much as the horn attaches with 12 AN470AD4 rivets to the parts, which provides a lot of structural integrity. Nevertheless, I intend to use NAS1097AD3 which has a smaller head. From what I understand, it provides less tensile strength, but again, the horn will not allow parts to separate. The shear strength might even be higher because of a shallower counter-sink.
Just in case, I asked Van's support to see what they think.
Now the parts are ready for etching and priming. I washed them with EkoClean.
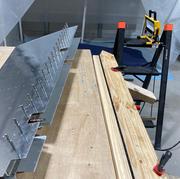
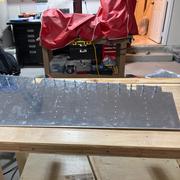
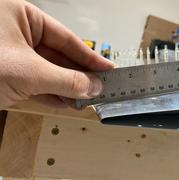
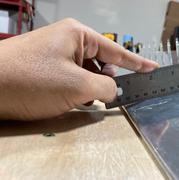
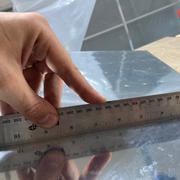
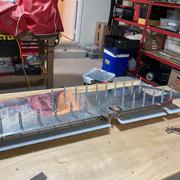
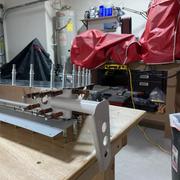
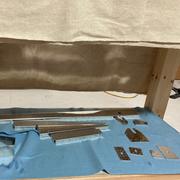