Bending the close-out elevator tabs
2h
August 26, 2025
A very stressful moment: bending the close-out elevator tabs!
Today I bent the elevator close-out tabs. There are a lot of reports of builders who had challenges with this procedure, so I tried to research as much as I can. The common issues seem to be blocks moving and cracks on the skin.
The manual suggests using wood bending blocks. Some builders make a bending brake, but I think it only works for the tab itself or the separate top and bottom skins, like in an RV-14. In an RV-7 I don't see a good way of clamping the brake.
So I went with the idea of bending blocks. As a first step, I re-did my bending blocks to make them wider so they have more friction.
For holding the blocks together, I tried using carpet double-sided tape to hold them in place (as somebody recommended), but I think it was the wrong tape: it only made parts slide easier as the glue of that tape was very gummy. Another idea I tried was to use a single-sided Gorilla Tape, thinking that it will increase friction. It did, but it adds some thickness, too. The most friction I got from a hot glue gun, but it is hard to get the hot glue to spread uniformly (and it adds a lot of thickness, too).
In the end, I decided to not use anything as blocks seem to stay in place with enough clamping force.
I did several test bends and found that if place blocks about 1/32" of an inch inside the bend line (deeper into the part), the bend line would be where I get the flat aluminum face. However, as it turned out later, I should have moved it 1/32" outside of the bend line (which is exactly what the manual says, duh). I don't know exactly why did I get the different results on the test pieces. Maybe, I was not hammering them hard enough with the rivet gun?
This is what the bending process looked like.
In the end, I got the line maybe 1/32" or 1/16" deeper than I initially thought. In the image below, the top blue line is where I anticipated the start of the bend (edge of the corner). As you can see, that line is on the corner. The bottom line was the line where I wanted to get the flat face of the aluminum. I did not check that line because it does not matter that much, the critical dimension was to get the bend line away from the relief holes enough that nothing cracks.
I think it worked out okay in the end. My concern was also the trailing side of the bend: initially, it looked like I would not get enough "meat" there for the bend. However, since I miscalculated the location of the bend line, it turned out to be just fine.
This is what the finished part looks like. I deepened the relief holes just a bit to get them away from the bend.
If I get perfect bends on the trim tab, I estimate the gap between the elevator and the trim tab to be about 1/8" (assuming the inboard edge and the trailing edges are aligned). This is just a 1/32" larger than the minimum gap of 3/32". Perfect.
Another concern I had is if the bottom tab pushed against the top tab bend and I got a crack there. There was a little scratch in the primer, so I removed the primer in that area and inspected the part as well as I could. I did not find any crack there.
Then I switched to the trim tab skin. I started rounding all the relief holes as best as I could, to minimize the chance of the skin cracking while doing the trim tabs.
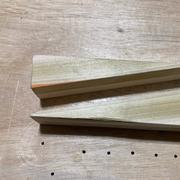
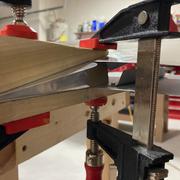
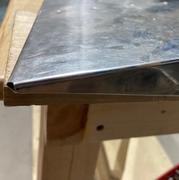
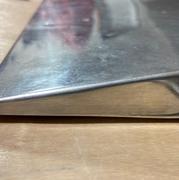
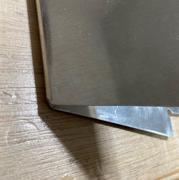