Riveting F705 together
6h
August 26, 2025
The final (for now!) step was to rivet F705 together.
Today I riveted F705 together. I only made one photo that depicts side channels being riveted to their doublers.
I squeezed every single rivet with my manual squeezer. I just get lazy to set up my pneumatic one, also, the manual one is easier to manipulate without scratching everything around.
The end result. I did manage to set 4 rivets I was not supposed to, so I carefully drilled them out.
Then I went to drill the holes in the plastic bearing blocks. Plastic tends to grab while drilling, so I wanted to drill the bushing blocks with as much control as I can have, which means using my milling machine. I measured the blocks with my caliper and got roughly the following measurements:
Both blocks were exactly equal, but the center hole was offset by ~0.015" from the center of the block. Which gave a ~0.030" difference between the edges of the hole to the edges of the block (which would be vertical offset in the installed configuration). So I decided to machine a "plug" that can go into the bearing hole of both blocks, centering them to each other so I can do more precise measurements.
This is me machining the plug on the lathe.
The are two mistakes here. First, you are not supposed to machine (especially, with the cut-off tool!) that far from the chuck: the part would flex, creating chatter. However, with a light cut and cutting oil, it went okay. I don't have soft jaws and I did not want jaws to leave mark on the part (since it is supposed to go smoothly into the 1" hole in the bushing blocks).
What was the second mistake? "Well, this is stupid" -- I thought to myself the moment the plug disappeared in the bearing block hole.
I forgot to double the depth of the hole (since the plug was supposed to go into both blocks). Luckily, the plug was thick enough that I was able to drill it at an angle, then pull it out with tools. Then I made another one, this time the correct length.
This is what two blocks connected together looked like.
As seen in the photo, the distance was about ~0.030". However, the two other sides were exactly flat. I put the blocks into the mill, used my edge finder to get 0.307" on the "short" side, then drilled the holes. The distance between two holes on the bulkhead channels looked like 1-5/8", so just I assumed that it was exactly that, 1.625".
The instructions suggest drilling with a #10 drill bit, but I did not have a #10 reamer, so I used by #12 reamer instead. The bolt is a bit tight but could be pushed with no issues. Everything matched just fine in the end.
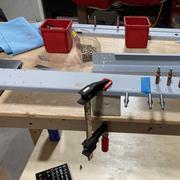
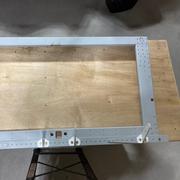
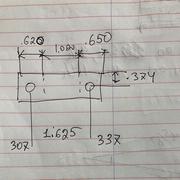
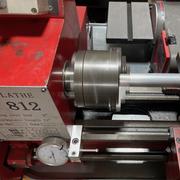
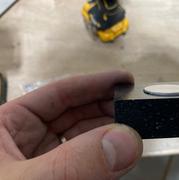
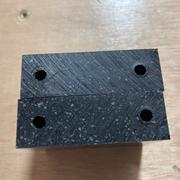
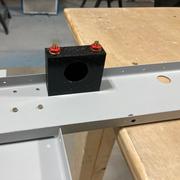