Finishing the right step
4h
August 26, 2025
Finished the right external step, and started the left one.
The next operation was to drill the plastic block that attaches the internal end of the step to the baggage rib.
I used my mill to locate and drill the #40 holes.
On the first block, I drilled all the way through the block. However, I found that the drill bit wandered a bit and the hole was not perfectly centered on the other side. So on the second block, I located and drilled the hole from both sides.
Then I put the block over the tube on the end of the step and drilled it to the baggage rib and to the tube itself. However, while I was opening the hole to the final dimension, I screwed up the hole in the plastic by tilting the drill bit.
So I decided to replace the block with the other one, and order a new one as well. Now the trick was to match-drill the second block, given that the tube was drilled already. After some measurements, I found that the misdrilled hole was on the side that I located on the mill, so the second block had the hole in the same location. After I upsized the hole to the #12 drill bit, the hole fit perfectly. Then I put it on the tube and upsized the baggage rib attachment holes by drilling from the baggage rib side. It worked well in the end.
This is the inside view of the skin where the step attaches. I probably need to open the hole just a bit more to allow for the welding fillets to fit.
Finally, I opened all the holes in the external step to #30. Initially, I tried using the #31 drill bit, but it did not work well. The drill bit would break almost immediately, not sure why. Probably, because it would grab the still, get too deep of a cut, and then break. The second drill bit broke exactly the same way.
So, I tried a different plan -- an old #30 reamer. Normally, I wouldn't use a #30 reamer in a #40 hole even in aluminum (reamers are only supposed to remove a very small amount of material), but I figured that it was worth trying. It worked quite well in the end. The poor reamer was really struggling (it would even visibly bend torsionally), but surprisingly, it did not break.
That concluded the fitting work for the right step.
After that, I switched to working on the left one. First, I drilled the hole for the step using the hole saw.
To expedite the trimming of the F-623 corner rib, I marked the locations of the cutouts from the same rib on the right side. Then I used my nibbler to cut the aluminum.
Shortened the pipe by estimating how much do I need to remove and using the block to mark the line.
Then I cut the tube using the hacksaw, and it was it for the day.
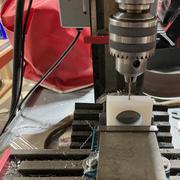
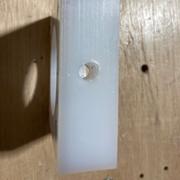
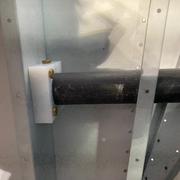
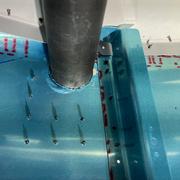

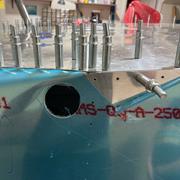
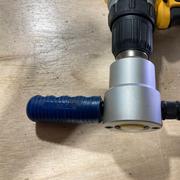
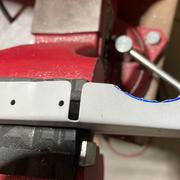
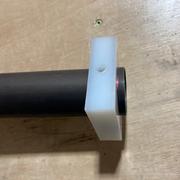