Fitting the right external step
2.5h
August 26, 2025
Today I worked on fitting the right external step.
Even though I am building a tail-dragger, I am installing external steps to help with entry. The first step in fitting the steps is to drill the skin. Per instructions, this step is done before the skin is bent. However, I figured that the hole would weaken the skin and make the bending process more difficult, so I did not drill it.
I mulled over different ways of drilling the hole without removing the skin and decided to use a hole saw. The exact size of the hole is not critical for the installation (besides, you need to enlarge the hole a bit anyway to make the weld fillets fit).
After slow and careful drilling, the hole is done.
After drilling the hole, I spend quite some time trimming the F-623 corner rib and the hole in the skin to make the step to fit better.
Then I put an estimated layout of the holes. I did not like the layout provided in the instructions. There are three holes in the skin already under the step, and the central one matches the pattern given in the instructions for the steps. However, the other two do not, which creates 7 holes total (5 holes for the step and 3 for the skin, with one hole being shared). Even though it kind of works in terms of edge distances, it still places rivets a bit too close. Also, the weld fillet would interfere with rivet heads, too. I don't know if the design of the step has been changed or what, but the filet is pretty wide.
Here is the original layout.
So after giving it some thought, I changed the second column of the rivets such that it reuses the three rivets in the skin. Then I drilled all the holes.
The layout is still not ideal, the bottom rivet (the top rivet on the photo) is kind of close both to the edge of the F-724 and to the next rivet. Note that all the holes are still #41 holes. I think it's okay, the edge distance is still more than 1.5D. However, on the left step, I will move the rivet just a little bit to improve the edge distance.
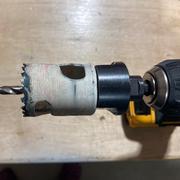
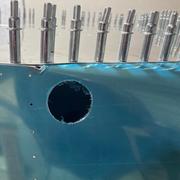
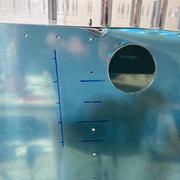
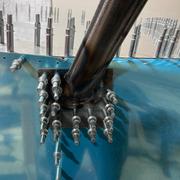
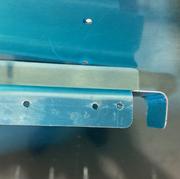