Fabricating the tiedown assemblies
4h
August 26, 2025
Over the last two days, I worked on the tiedown assemblies.
Since I don't like match drilling the holes for the bolts, I decided to drill as much as I could on my mill. I guesstimated the distance between the holes on the wing spars to be 1.5". The thinking here is the same: if the dimension looks like a "round" one, it likely was exactly that in the CAD model.
I put the spacer blocks in the mill and drilled/reamed the holes for the bolts. After doing the first block, I tested it against the spar, and it was a perfect match.
Then I drilled the tiedown bars themselves. First, I guesstimated the horizontal distance between the holes to be 1.250", and then I drilled the two holes in the bars. I did not drill all four because I wasn't sure I could guesstimate the distance from the top holes to the bottom holes.
Two holes were enough to lock the bars well against the spar (after making sure they were vertical). Then I used brass tubes to match-drill the other two holes and lock the bars to the spars with the bolts.
The next step was to match-drill the holes from the spars to the tiedown bars. I slid the spacers between the tiedown bars and the spars for better alignment of the brass tubes.
The intermediate result.
Then I threaded the bars with a 3/8-16 tap. Wasn't overly dramatic. First, I cleaned the hole to 5/16", which is what I have in my drill tables for 75% thread 3/8-16. I probably could have tapped the holes without drilling them, the drill didn't really increase hole size by a lot.
I checked all the boltholes against the spars, and they fit nicely. The holes in the spars were left exactly the way they were, at no point I was drilling through them with the full-size drills (only through brass tubes inserted in the holes).
Then I cut the lightening holes in the spacers. I had a 1" hole saw but decided to use a 7/8" instead. A 1" saw would have cut oversized holes (it wasn't really a saw for metal, just some hole saw from Home Depot I had).
Also, I drilled the holes for the nutplates using the specification of the K1000-3 nutplates (their holes are spaced at 11/16").
Finally, primed the parts.
And assembled them with the nutplates. I did some test fitting, and everything fits nicely
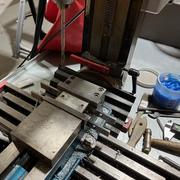
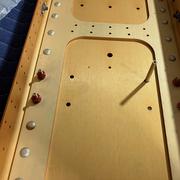
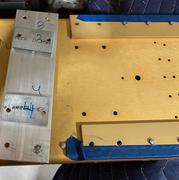
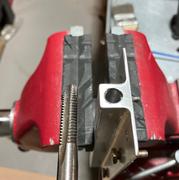
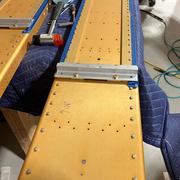
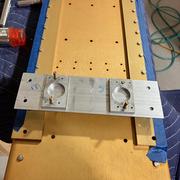
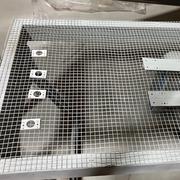
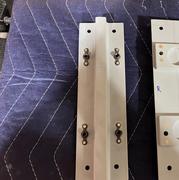