Riveting the left aileron
5h
August 26, 2025
Today was a long session riveting the left aileron.
The first steps were to cleco everything and match-drill, plus upsize the bottom holes to #30 for the CS4-4 rivets.
One of the steps was to use a long drill bit to drill the nose rib flange to the counterbalance pipe. While doing that, my drill bit wandered, and I elongated the hole in the flange.
My mistake was to start drilling at a high speed -- instead, I should have started slow, which would create a good starting dimple in the pipe.
So I took another A-704-L nose rib (the one that was supposed to be for the right aileron) and continued.
Then I started assembling everything. The first rivet was an LP4-3 rivet to attach nose ribs to the counterbalance pipe. They are set with ribs bent away to be able to access the rivet with the rivet puller.
Then I riveted the skins to the top flange of the spar. I wrapped my bucking bar with some tape to raise its front part. With the back of the bar resting on the bottom flange of the spar, the slanted front end of it is exactly perpendicular to the top rivets.
With the bar positioned like that it was very easy to set all the top rivets. I had to drill out only one rivet, and only because I didn't push it enough with the rivet gun.
Then I buck a number of rivets on both the nose and the main ribs. As per tradition, the aftmost rivets on the main ribs were hard to set due to limited access. However, it turned out, one of my bucking bars worked perfectly for that.
Here is what the bucking bar looks like:
Finally, I pulled all the CS4-4 rivets, the ones that attach the counterbalance to the leading edge and the ones that are on the bottom of the aileron.
Also, it is not depicted, but I bolted both brackets to the aileron. Torqueing bolts to the specification was a bit of a challenge due to very poor access to both bolt heads and the nuts. One bolt I had to torque by "feel" since I wasn't able to put my crowfoot adapters on the nut.
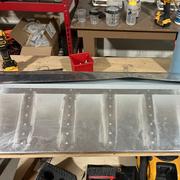
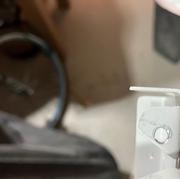
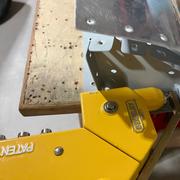
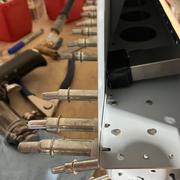
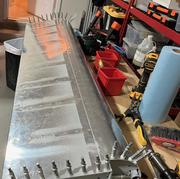
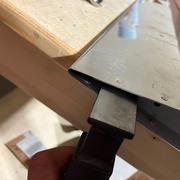
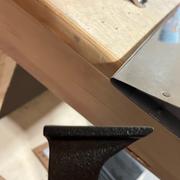
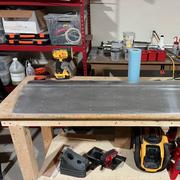