Fabricating the rudder pedals bearings
4h
August 26, 2025
In the last two days I worked on new bearing blocks for the Contral Approach rudder pedals.
Even though the blocks supplied in the kit fit the Control Approach rudder pedals, I decided to machine my own bearing blocks to unify the fastener spacing between the outer bearing blocks and the center one.
The size I came up with is a block that is 3/4" thick, 2" high, and 2-3/4" long. This provides about 3/8" edge distance for the central block (it has a 1-1/4" hole) and 3/8" edge distance between the bolt holes and the edges / central hole.
To make the blocks I got some Delrin (acetal), which has low friction, is wear-resistant, strong, and machines well. The original bearing blocks use UHMW, however, which seems to have better wear resistance. Will see.
Blocks are cut and machined to size.
The next step was to bore the hole for the rudder pedals. This hole, however, needs to be at an angle, as the fuselage gets wider from fore to aft. I tried different ways to measure that angle, which came at about 1.8° degree (3.6° included). The ultimate way I used is I measured the angle on the original blocks.
I had a 1" plug which I used to connect two blocks together. Then I measured the gap between them, which turned out to be 1/4", which gave me a 1/8" offset for the 4" long block, or 0.086" for a 2-3/4" long block.
Then I machined a simple fixture to offset the block in the vise. Like a primitive sine plate. It came out at 0.088".
This is how the offset is used: it lifts one side of the bar to be machined to get the required angle.
I used an end mill to drill the initial hole of 3/4".
Then I continued with the boring head to upsize the hole to about 1.004", which was the diameter of the tube.
The depth of the hole on the "deeper" side is 0.650". I positioned the cutter over the block, lowered it until it touches the bearing on the "high" spot, then marked that as a zero on my indicator. Bored to the depth of the 0.650".
The blocks fit well, angle-wise. Not too loose, not too tight. There is some amount of friction, probably, because my holes are not round and the tubes are not round, too. For some reason, my boring head cuts ovals, maybe, because the head of my mill is out of alignment or something like that.
Finally, I fabricated the central block. To avoid the need to use the washers because of the split line, I used the following procedure. First, I drilled the bolt holes so I can use them later for alignment. Then, I split the block with the slitting saw. Finally, I put the halves together with bolts used for alignment, clamped it in the vise, and bored the hole (1-1/4") through it.
The final height of the block is a bit shorter than 2" (because of the slitting saw thickness), but not by much.
The bearing block around the tube.
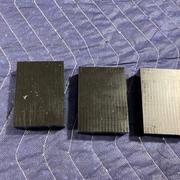
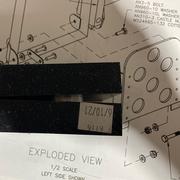
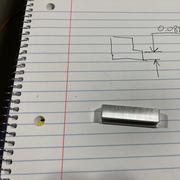
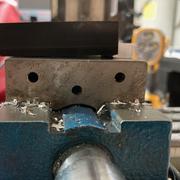
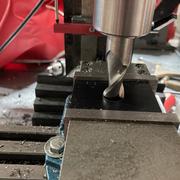
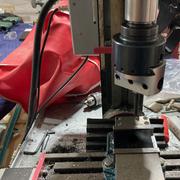
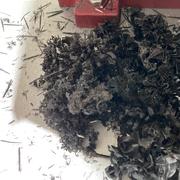
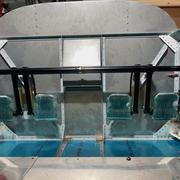
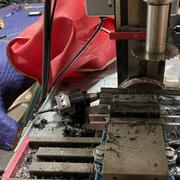
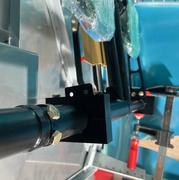